The American Advanced Robot Manufacturing Innovation Agency funded six new techn
According to a report on the official website of the American Robotics Innovation Institute for Advanced Manufacturing (ARM) on August 12, 2024, the institute has selected six new technology projects for funding from the 24-01 batch of technology project solicitations, aiming to address a wide range of manufacturing challenges through robotics and artificial intelligence. ARM plans to provide $2.9 million in project funding, with a total investment of approximately $6.1 million for the six new technology projects.
The 24-01 batch of technology project solicitations mainly focuses on the following thematic areas: multimodal input for intelligent robots in manufacturing, rapid task reconfiguration and quick response of robots, multi-robot, human-robot collaboration, and virtual commissioning of advanced robotic systems.
Here is a brief description of the six funded projects:
1. T-Shirt Automated Production System
Led by Henderson Sewing Machine Company, with the participation of Hanbai Company, Apparel Robotics Company, Southwest Research Institute, Interface Technology Company, and Massachusetts Robotics Company.
Advertisement
The apparel manufacturing industry is an industry with high automation demands and is also a strategic focus of the ARM Institute, which has funded several robotic projects in the field of apparel manufacturing. This project will develop and test a robotic system to automate six steps in the T-shirt production process, demonstrating the feasibility of automated garment sewing in a manufacturing environment.
2. Rapid TPC Welding Technology for Scaled Production
Led by Raytheon Technologies Research Center, with the participation of Carnegie Mellon University, Wasson Technologies LLC, and Collins Aerospace.
Lightweight carbon fiber-reinforced thermoplastic composites (TPCs) are a key material that can meet the rapid production needs of the future aerospace market. Welding is a challenging but crucial step in the rapid production of TPCs. In a previous ARM-funded project "Rapid Welding of Thermoplastic Composite Structures," continuous ultrasonic welding of robots was proven to increase induction speed. This project will expand on the previous project to achieve production application.(III) Robotic Assembly and Manufacturing Environment (FRAME) 2.0 without Fixtures
Led by Lockheed Martin, with the participation of the University of Southern California, Carnegie Mellon University, and Yaskawa Electric Corporation in research.
Building upon the outcomes of previously funded projects by ARM, this project aims to construct a fixtureless manufacturing cell for high-mix/low-volume (HMLV) production. Characterized by human-robot collaboration, it is designed to enhance efficiency, reduce downtime, and increase cell output. The project will focus on addressing challenges related to larger part sizes and more complex assembly scenarios, advancing the project to a production line pilot.
(IV) Adaptive Robotic Installation of Automotive Parts Using Multimodal Artificial Intelligence (AI)
Led by ThoughtForge AI, with the participation of Siemens and Magna International in research.
In the automotive, aerospace, and consumer electronics industries, real-time force application and adjustment are required for the installation of asymmetrical and oddly-shaped objects, with adaptive installation operations typically performed manually. The key to achieving an autonomous adaptive installation system is multimodal AI, which combines real-time sensor information, machine learning techniques, and edge computing technologies to accommodate the installation of parts of various shapes, sizes, and weights across different industries. The project aims to integrate multimodal AI inputs, machine learning algorithms, advanced computing technologies, and sensors into a robotic system, enabling it to be flexibly applied to a wide range of adaptive installation scenarios.
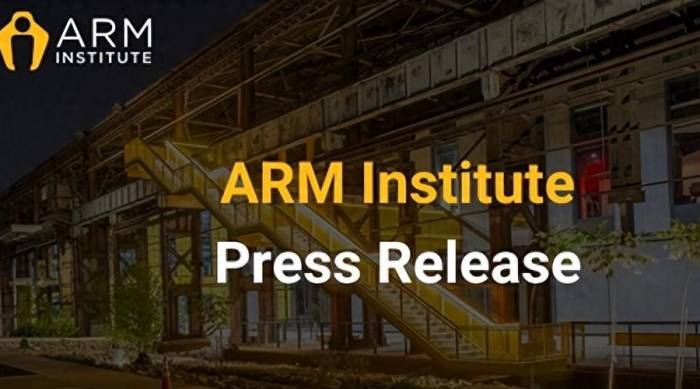
(V) Automated Finishing System for Castings
Led by CapSen Robotics, with the participation of Ohio State University, Southwest Research Institute, and Yaskawa Electric Corporation in research.
Metal casting offers great flexibility in component size, shape, and material and often operates in a HMLV manufacturing mode. Castings tend to have highly variable features and defects, with the finishing process currently relying on manual labor. This can lead to errors, increased costs, and slower speeds. The project team will develop an autonomous robotic finishing system. This system will image castings, reconstruct 3D models, identify parting line burrs, create tool paths and motion plans for grinding operations, and perform robotic grinding—all with minimal human intervention and without the need for explicit CNC programming.
(VI) Path Planning for Rapid Robotic Response to Spraying Complex Geometries
Led by [Name of the leading organization], with the participation of [Names of participating organizations] in research.
[Details of the project, including its objectives, the challenges it aims to address, and the innovative aspects of the research, should be provided here.]The project is led by Northrop & Grumman Corporation, with Manufacturing Automation Systems and Ohio State University participating in the research.
In the defense industrial base, the current high-precision, large-scale, and complex robotic coating applications often struggle to ensure a high first-pass yield, which can lead to excessive manual rework, reprogramming, and delivery delays. Ensuring uniform coverage of coatings and preventing material from being sprayed onto other areas when applying coatings and finishing complex geometric parts is a technical challenge. The project team will develop autonomous robotic path planning software, utilizing metrology measurement data, to plan robotic paths for the coating and finishing of complex geometric parts.
Source: Robotics Technology and Applications